Ensuring optimal truck performance is quite simple. The key lies in regular maintenance checks, spotting issues before they escalate, tracking fleet status, and implementing preventive strategies. Routine maintenance and service secure minimal downtime, better productivity, and security. Expert guidance from experienced technicians will guide you through fleet maintenance through the smart implementation of tech solutions, thorough documentation, and qualified staff. Dive into this comprehensive guide to fleet maintenance and unlock economical operations. There's much to explore and uncover!
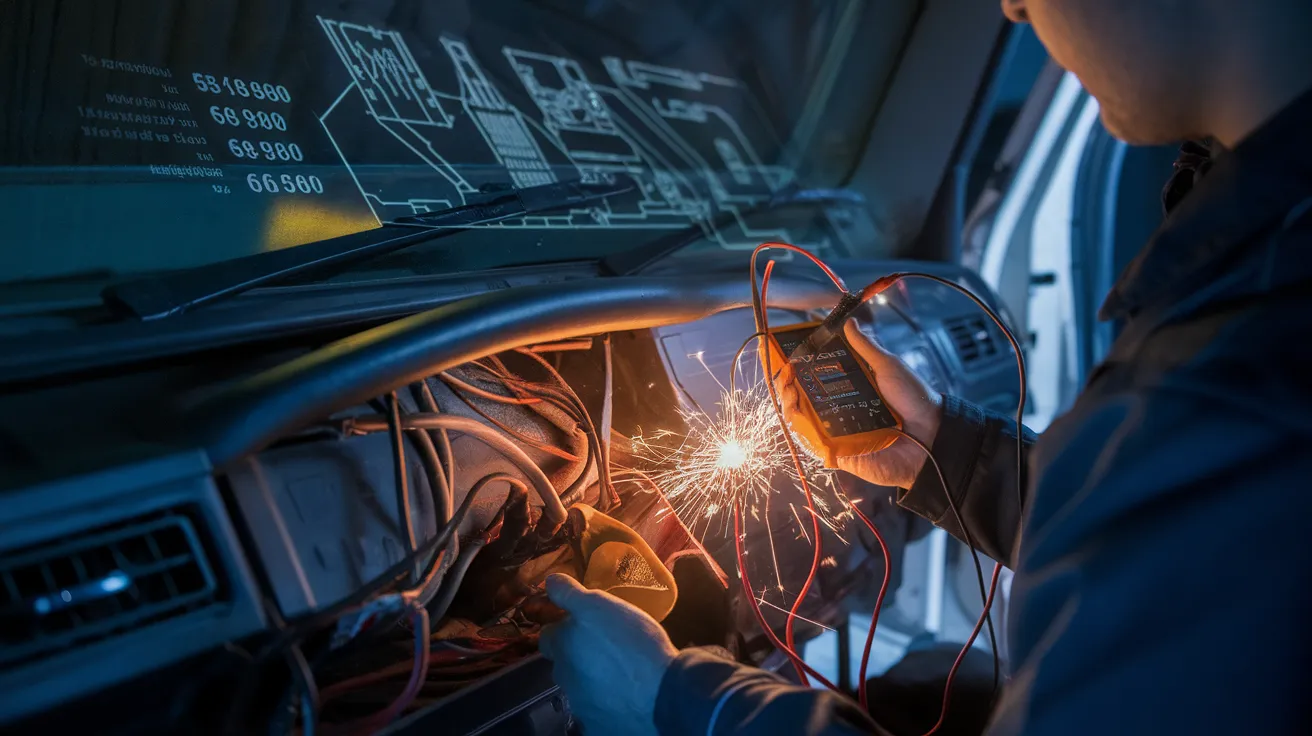
Main Insights
Grasping the Importance of Routine Truck and Fleet Maintenance
While it may appear challenging, mastering proper fleet and truck maintenance is vital for any thriving operation. You'll discover the maintenance benefits far exceed the resources you put in. Routine inspections and maintenance can greatly increase your vehicles' longevity, saving you from costly replacements. Plus, there's an undeniable connection between regularly maintained fleet and better fuel economy. This translates to lower fuel costs, boosting your bottom-line performance. Additionally, frequent maintenance can help identify small problems before they become serious problems, preventing costly repairs later on. Thus, don't overlook the power of scheduled servicing; it can be a significant factor for your company's profitability.
Recognizing Key Components of a Well-Planned Maintenance Program
To ensure your fleet's efficiency and durability, it's critical to recognize the fundamental aspects of a well-designed maintenance program. You'll must comprehend the essential elements of maintenance, assess the health of your fleet periodically, and put in place preventive measures ahead of time. With these in place, you're positioned to reducing downtime and enhancing productivity.
Fundamental Program Maintenance Aspects
If you're looking to boost your fleet's productivity and longevity, implementing a robust maintenance program is essential. Critical elements of the program encompass scheduled inspections, routine servicing, and preventive repairs. Each of these elements is essential in minimizing expensive failures and limiting downtime. While the advantages of a maintenance program are substantial, you must consider the obstacles to implementation. These can range from operational difficulties and team reluctance. Nevertheless, with careful preparation, effective messaging, and focus on skill development, these obstacles can be addressed. Don't forget that an well-designed maintenance program isn't just about repairs; it prevents them. It's an commitment in your fleet's longevity – and it's one that will yield significant returns.
Asset Performance Monitoring
When examining the key elements of a well-designed maintenance program, recognizing the importance of fleet condition monitoring takes center stage. It's not just about keeping your vehicles running, it's about optimizing fleet performance. Vehicle tracking solutions deliver a complete view of your fleet's condition, empowering you to identify potential issues before they become serious.
Such tracking solutions measure key metrics like fuel performance, tire conditions, engine status, and more. Through analyzing this data, you're not only ensuring the longevity of your fleet but also reducing unnecessary repair costs. Keep in mind timely more info discovery is key in fleet management. Thus, adopt reliable monitoring technologies and remain ahead of the curve. Don't just react to problems, forecast them. Monitor your fleet's status regularly and your enterprise will operate efficiently.
Setting Up Preventive Strategies
While monitoring your fleet's condition plays a vital role, implementing preventive measures is equally important to ensure a successful maintenance program. You must detect potential concerns before they transform into costly repairs or downtime. Let's explore preventive maintenance approaches.
An important approach is developing a detailed maintenance checklist. This checklist should specify all necessary inspections, maintenance procedures, and component updates. Periodic engine inspections, tire rotations, and oil changes are fundamental. But don't overlook minor components like wipers, lighting systems, and filter components.
Your maintenance plan needs to include a timetable for all maintenance tasks. Sticking to this schedule ensures that your fleet remains in peak condition. Keep in mind, preventative care cuts down on expenses, time, and problems in the future.
Critical Regular Inspections for Commercial Vehicle Management
To ensure your truck and fleet stay in optimal condition, you need to prioritize regular maintenance inspections. These checks encompass routine maintenance checks and essential system reviews. By maintaining these vital protocols, you'll maximize your fleet's longevity, improve operational performance, and in the end, save on costly repairs.
Periodic Maintenance Reviews
Regular maintenance inspections represent your best protection from unplanned vehicle and fleet malfunctions. They provide you an opportunity to spot and address problems before they develop into costly repairs or dangerous accidents. One of the most significant benefits of routine maintenance is the prevention of downtime, which can significantly affect your operation's performance and revenue.
Key Component Evaluations
Expanding upon the critical nature of scheduled maintenance inspections, let's move towards the particular essential component checks that ought to be carried out regularly to guarantee peak truck and fleet performance. Start with the brake system – confirm all components are operating correctly, from brake pads to fluid levels, and checking for leaks. When overlooked, brakes might fail, leading to catastrophic incidents. Tire pressure checks are equally crucial. Insufficient pressure increases fuel consumption and tire wear, while over-inflation may lead to a blowout. Invest in a high-quality pressure gauge for precise readings. Remember tires should be cold during checks for optimal results. Regularly performing these essential checks can prevent costly repairs and potential accidents. Drive safely on the road.
Essential Fleet Maintenance Practices for Peak Performance
When managing a fleet, it's essential that you focus on preventative maintenance to maintain peak efficiency. Implementing a systematic preventative scheduling system is essential. This minimizes unnecessary wear and tear, and reduces the probability of unscheduled downtime. You must arrange regular inspections and maintenance based on engine hours, mileage, time, or fuel usage. Note that each vehicle is distinct and could require a tailored approach.
Maintenance education serves as a crucial approach to maintain peak efficiency. Equip your team with the necessary skills to identify potential issues early on. This saves both time and effort but also minimizes expenses. The integration of maintenance training and preventative scheduling will create a highly effective and dependable fleet. Proactive maintenance always trumps reactive repairs.
Essential Tips for Commercial Vehicle Service and Rehabilitation
Although truck and fleet repair and restoration might appear challenging, knowing the basics can help simplify things. The first thing you should do is to learn about multiple restoration approaches. This knowledge will help you identify problems quickly and efficiently. Then, arrange maintenance work according to the extent of repairs needed and the unit's importance in your vehicle lineup. Routinely examine each vehicle for developing concerns and address them promptly to prevent further damage. Don't forget, renovation isn't simply problem-solving, it's aimed at upgrading the vehicle's functionality and longevity. Lastly, always use top-grade materials for repairs; they'll provide better durability and performance. Remember these guidelines, and you'll navigate vehicle fleet repairs and upkeep with ease.
Leveraging Technological Advances for Advanced Fleet Management
To maintain a competitive edge in the trucking industry, it's vital to leverage industry innovations for advanced fleet maintenance. New technologies are rapidly changing the maintenance landscape. Embrace data analytics to monitor your fleet's operations and predict potential issues in advance.
Advanced real-time tracking systems keep track of engine conditions and status, fuel consumption, and driver behavior patterns. Utilize this crucial data to schedule predictive maintenance, minimizing expensive downtime.
Don't overlook software updates. They usually deliver crucial modifications that boost your fleet's performance and safety. Keep in mind fleet maintenance isn't limited to mechanical care. You're operating in a digital age, and keeping up with industry innovations will help ensure your fleet's sustainability and revenue generation. Through the right solutions, you'll reduce time and money, and safeguard human life.
Frequently Asked Questions
What Requirements Must an Expert Fleet Service Technician?
You must have an official certification, fulfilling the requirements of an established mechanic institution. Moreover, you'll need a comprehensive skill assessment, proving your knowledge in multiple facets of fleet repair and maintenance. Experience counts too!
What's the Right Time to Replace Fleet Vehicle Tires?
As the seasons change, you should regularly check your fleet's tire wear periodically. However, it's generally recommended to install new tires every three to six years, according to usage and road conditions.
What Are the Common Signs of Engine Trouble in Trucks?
You'll spot truck engine problems via symptoms like strange engine sounds or poor fuel performance. Other signs include unusual exhaust smoke, fluid leakage, or possibly a continuously lit check engine warning.
What Role Does Technology Have in Modern Truck and Fleet Maintenance?
Technology is crucial in improving truck maintenance. Advanced monitoring provides real-time data, while analytical tools forecast issues before they happen. You'll experience reduced downtime, better safety measures and ultimately, cost savings. It's revolutionary.
What Maintenance Considerations Apply to Different Types of Fleet Vehicles?
Various vehicles need unique maintenance schedules. One must account for the intended use, carrying capacity, and operating terrain, as these elements greatly influence required servicing. Make sure to tailor maintenance according to the vehicle category.
Conclusion
In the end, what matters most is ensuring your fleet operates efficiently, wouldn't you agree? Routine maintenance isn't merely a recommendation, it's a must. By pinpointing crucial elements, carrying out systematic evaluations, implementing proactive measures, and harnessing industry innovations, you're doing more than basic maintenance, you're developing a high-performance fleet. And don't forget, truck and fleet repair isn't a failure, it's an opportunity for restoration. Stick with it, and you'll witness your fleet's efficiency, reliability, and longevity achieve new levels.